In the world of CNC machining, it’s important to know the differences between various techniques if you want to get the best production efficiency and accuracy. Two popular methods are 3+2 axis machining and five-axis machining, and these are widely used in industries like aerospace, automotive, and medical. But they operate quite differently, so let’s break down what sets them apart and when you’d want to use each one.
Understanding 3+2 Axis Machining
3+2 axis machining is a method that combines regular 3-axis movement with some rotational capabilities. In this setup, the machine can tilt or rotate the workpiece in one direction at a time, letting the cutting tool approach the piece from different angles. This is similar to how 3-axis machining works after the part has been set in place. One big perk of using a 3+2 setup on a vertical machine is the ability to machine a piece from multiple sides, which cuts down on the number of setups needed. This ultimately helps speed things up and reduce costs. Plus, it often allows for the use of shorter, sturdier cutting tools, which improves tool stability and lifespan.
But keep in mind, 3+2 axis machining is a single-stage process. You first secure the workpiece in a certain position, then the machine adjusts the angle using its rotational axes before going back to the standard three linear axes (X, Y, Z) to finish the job. This approach is good for working on complex shapes and surfaces but doesn’t offer the same level of continuous movement that you get with true five-axis machining.
The Advantages of Complete Five-Axis Machining
On the flip side, true five-axis machining, also known as simultaneous 5-axis machining, lets the CNC machine move the cutting tool or workpiece across five axes all at once. This ability is what makes it possible to create super complex components, unlike 3+2 axis machining, where the part stays still while the angles change. While 5-axis machines can also use shorter tools for better support and less bending, this leads to faster cutting speeds and longer tool life, which can lower costs on tool replacement.
With 5-axis machining, the cutting tool can continuously interact with the workpiece without needing to stop and adjust things manually between different processes. This not only speeds up production but also improves the quality of the surfaces being finished and enhances precision. 5-axis setups are perfect for making detailed components used in fields like medical, oil and gas, and aerospace.
Key Differences and Choosing the Right Method
The main difference between 3+2 axis and full five-axis machining lies in how they operate. 3+2 axis machining gives better access to different surfaces of a workpiece without needing the continuous movement that five-axis systems provide. This often makes it a more budget-friendly option. On the other hand, five-axis machining can move continuously across all axes, offering top-notch precision for more complex parts, but it usually costs more and might require some specialized knowledge.
When picking between these two methods, manufacturers need to think about their specific needs. For pieces that have intricate shapes but don’t need constant movement, a 3+2 axis machine works great. However, if you’re dealing with really complex parts that need precise shapes and tolerances while moving all the time, then five-axis machining is the better route to take.
Pricing: 3+2 vs. 5-Axis CNC Machines
When it comes to the cost of CNC machines, used ones can be a great way to get into advanced machining without breaking the bank. You can usually find a used 3+2 axis machine priced between $45,000 and $125,000. Popular brands like Haas or Fadal may have machines in the $60,000 to $85,000 range if they have been well cared for. This lower initial investment makes 3+2 machines appealing for shops wanting to improve their capabilities without spending a ton of money.
In comparison, used full five-axis machines usually start around $85,000 for older models and can go up to $250,000 for well-maintained options from brands like DMG MORI or Mazak. The higher price tag is due to more advanced control systems and components needed for simultaneous operation.
If you’re considering used machines, keep in mind some additional costs. You might need to budget for things like retrofitting (around $10,000 to $30,000), installation (about $5,000 to $15,000), initial maintenance (around $3,000 to $8,000), and operator training (which can run $2,000 to $5,000 per person).
Conclusion
To sum it up, both 3+2 axis machining and five-axis machining have unique benefits for different manufacturing needs, but they do operate in very different ways. 3+2 machining is a solid middle ground, balancing cost and improved functions, and works well for pieces with complex shapes that don’t require constant movement. Meanwhile, five-axis machining shines when it comes to precision and flexibility, making it the go-to choice for highly detailed and accurate applications.
By understanding these two methods better, manufacturers can make smart choices about which CNC setup fits their specific needs. Whether you go for the budget-friendly 3+2 axis machining or the precise 5-axis option, the right choice can really make a difference in production efficiency, costs, and overall quality.
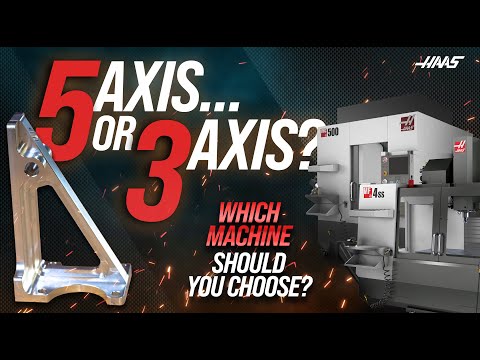