Since its origin, manufacturing has revolutionized itself in waves. The first industrial revolution brought the advent of steam and coal to manufacturing, followed by the introduction of electricity and then information technology. In this day and age, what can we expect to enter the manufacturing arena next?
The fourth industrial revolution has actually already begun—and it’s called Industry 4.0. So what does that mean for CNC machining and manufacturing as a whole? How can shops and workers prepare? How should they adapt to the new wave of technology?
We’re breaking down Industry 4.0, what it really means and how businesses can train their staff and embrace this new era of industry.
What Is Industry 4.0?
Industry 4.0 refers to the fourth industrial revolution. This revolution uses data and cloud computing for production and manufacturing. The Internet of Things, specifically the Industrial Internet of Things (IIoT), along with artificial intelligence and computer integration are the core components of Industry 4.0.
These new technological developments automate many processes of manufacturing, creating a “smart” facility. Each system can communicate with each other and share data, which results in quicker turnaround times and savings on costs.
The Internet of Things
The Internet of Things (IoT) is a network of objects or items that are connected to the internet and are able to share data with each other. The Internet of Things can be used at home with smart lighting and thermostats, in cars with sensors to promote safe driving, in the office with connected alarms and in the industrial manufacturing space.
The shared, real-time data automation was once a manual process and extends throughout the entire manufacturing process, from product design to gauging customer satisfaction. All of this integration and digital technology creates smart factories and CNC machine shops, with improved productivity and decreased downtime.
The Driving Factors of Industry 4.0
There are three driving factors for Industry 4.0:
- Integration
- Data collection
- Customer success
These drivers share two things: data and analysis. The goal of all this interconnectivity is to automate and streamline processes, which can’t be done without the proper data collection and analysis. It’s more than just a way to manage your CNC machine shop; it’s a way to run your entire business.
Industry 4.0 relies on digital technology to function, specifically instruments and machines that can sense, monitor and respond autonomously to physical processes. A few examples of this are GPS sensors for fleet tracking, smart sensors that monitor system performance and analytics that help machines self-diagnose issues.
Standards for the IIoT on the Shop Floor
As you might have guessed, having so many different smart devices on a shop floor could create issues if not properly addressed and regulated. That’s where manufacturing standards and protocols come in. These standards control how CNC machines communicate and share data with each other.
These technical standards define data tags and behavior for software. Like other tech regulations, they standardize and promote interoperability between machines. Simply put, it helps all of the machines at your business work efficiently.
These manufacturing standards and protocols also enable you to effectively monitor cycle time validation, error handling and machine utilization throughout your shop. You’ll have visibility into all of your machines to boost overall efficiency.
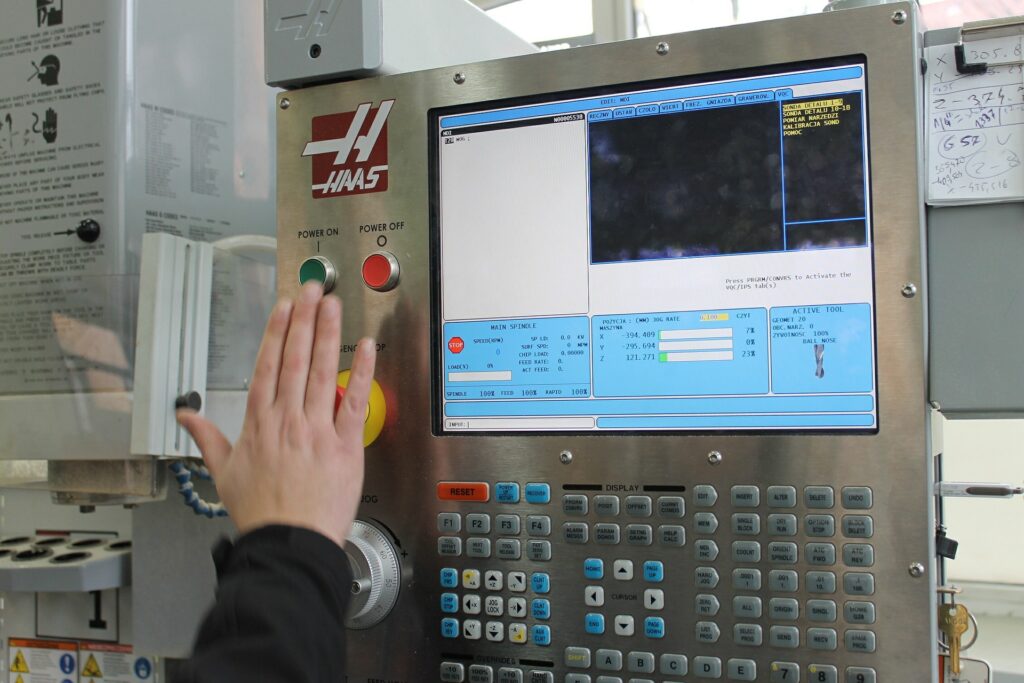
How Industry 4.0 Is Changing CNC Machining
Industry 4.0 is changing how CNC machine shops run on a day-to-day basis. With all of the smart technology and integrated software available, quicker turnaround times and decreased downtime all result in increased productivity.
Data collection and analysis from sensors and other instruments help CNC shops test out new products or study product use. Customer satisfaction is the main goal, and testing and refining the product with data will only result in a better end product.
Industry 4.0 is only the latest in industrial revolutions. Data helps inform CNC machine shops and manufacturers alike on how to make better products their customers will absolutely love. It also allows business owners to examine their supply chain management process and delegate dangerous or tedious tasks to the machines. Having all of these data points will accelerate manufacturing and CNC machining as a whole.
While this type of automation can help prevent injury and increase your shop’s productivity, these computer systems do still require operators to use them. You may also need to bring on IT workers to help maintain these new systems.
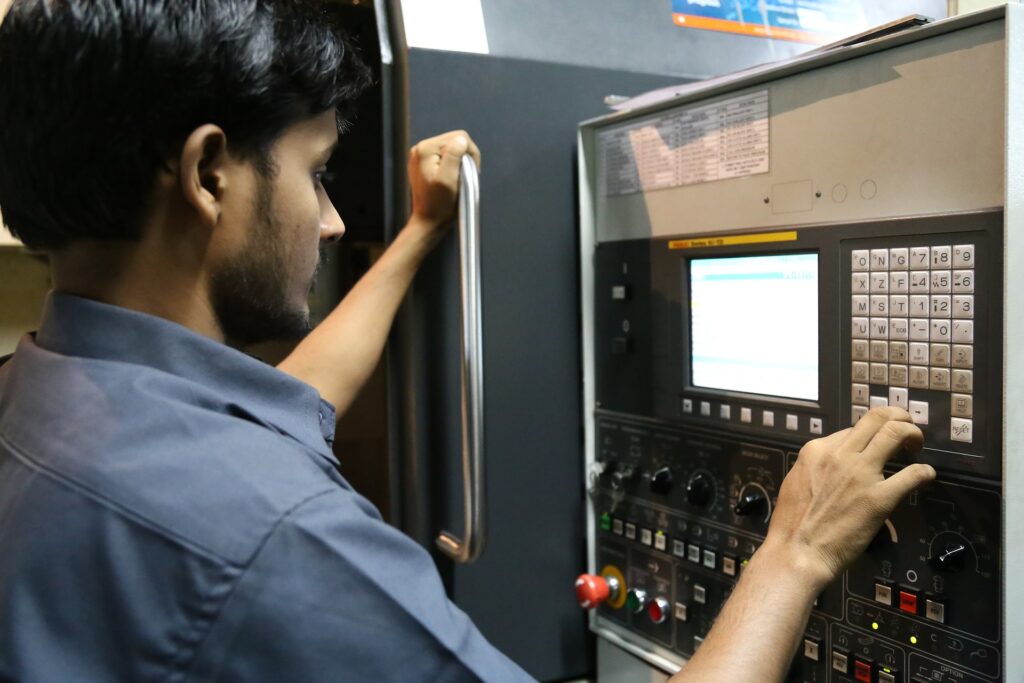
Embracing Industry 4.0 at Your CNC Machine Shop
Industry 4.0 technology is disrupting the manufacturing space. Bringing connectivity and data collection to the forefront, the IIoT brings increases productivity and can lead to overall higher customer satisfaction. Getting your CNC machine shop up to speed and implementing these changes will require training, time and patience.
Training your current employees on these new systems and tools will help ease them into the transition. These new computer-based systems require monitoring and will need to be operated by a person, so educating and preparing your staff must be a priority as you embrace this new digital transformation. Having all of your employees on the same page and trained enough to properly use these new pieces of technology will help decrease downtime caused by errors.
Conclusion
Industry 4.0 is the latest wave of change for manufacturing and commerce overall. The integration of new technology and embracing of data can create much more efficient processes for manufacturers and CNC machine shops alike. While the use of the IIoT becomes more widespread, it’s up to shop owners to train their staff on this new technology.
Instead of fearing this change as the potential obsolescence of the worker, Industry 4.0 is an opportunity to bring new efficiencies and improvements to already-existing processes. These new machines still need workers to monitor and operate the system—in fact, you may need to hire an IT team to help with any software issues that arise. Industry 4.0 is an industrial revolution in progress and it’s one that CNC machine shops can use to meet and exceed their goals.