What is a CNC Machine?
Complete Guide To Computer Numerical Control Machines
CNC stands for computer numerical control machine, a crucial tool in computer-aided manufacturing (CAM), utilizing computer programming to automate the movement of machine parts. Unlike traditional machines that require manual operation, CNC machines interpret digital designs to execute precise cuts, shapes, and actions on various materials such as metal, wood, and plastics.
The technology behind CNC machines significantly enhances manufacturing efficiency, consistency, and precision, making them essential in contemporary production environments. These machines come in various complexities, from simple lathes to advanced multi-axis machining centers, catering to a wide range of industrial needs.
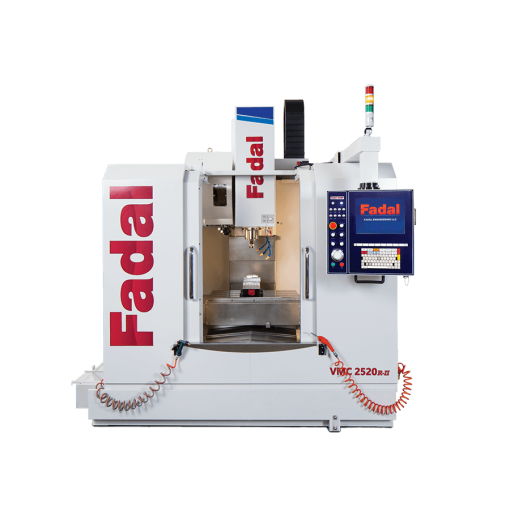
History of CNC Machines & Machine Tools
Creation of CNC Machines
The evolution of CNC machines is intertwined with the broader advancements in technology and automation throughout the 20th century.
Early Beginnings
The concept of numerically controlled machines dates back to the 1940s, when the first implementation involved using punched cards to control the movement of machine tools. In 1952, a pivotal moment occurred when John T. Parsons and his team at the MIT Instrumentation Laboratory developed the first true NC (Numerical Control) machine, which significantly enhanced precision and repeatability in manufacturing processes.
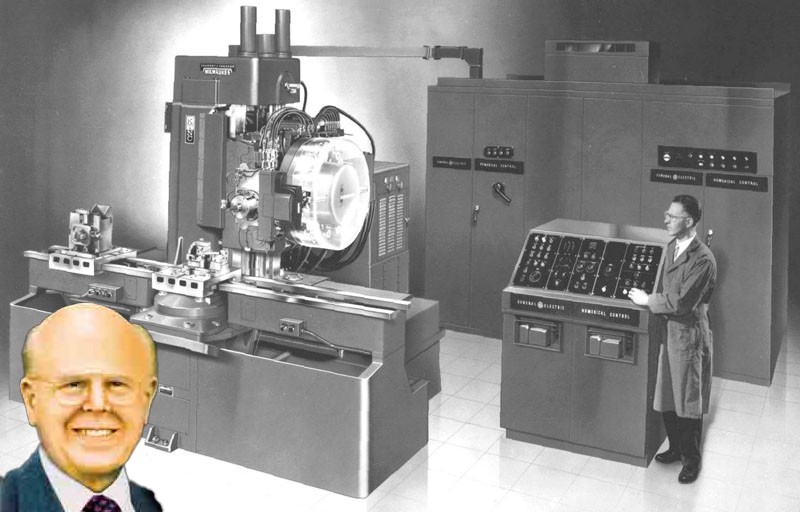
The Rise of Computer Technology and Revolutionizing Precision with Microprocessors
By the 1960s, significant technological advancements paved the way for the introduction of computer technology into manufacturing, giving rise to Computer Numerical Control (CNC) machines. This era marked a transformative shift from traditional punch cards to digital computers, which allowed for more sophisticated programming and control mechanisms, leading to greater automation in production processes. The integration of microprocessors in the 1970s further revolutionized CNC technology, empowering machines to execute complex tasks with unprecedented accuracy and efficiency. This evolution not only enhanced precision in manufacturing but also set the stage for the modern automation landscape we see today.
Increased Accessibility in the 80s and 90s
As CNC machines continued to develop throughout the 1980s and 1990s, they became significantly more accessible and affordable for various industries, including manufacturing, woodworking, and metalworking. This period marked a pivotal shift, as the introduction of user-friendly software interfaces transformed the landscape of CNC operation. These interfaces were designed to be intuitive, enabling not only skilled machinists but also operators and designers with limited technical backgrounds to engage with the technology effectively.
With these advancements, users could create intricate designs and automate complex production processes without the need for extensive programming knowledge. This democratization of CNC technology led to an explosion of creativity and innovation, as more individuals and small businesses were able to leverage these tools to bring their ideas to life. Consequently, the 80s and 90s paved the way for a new era in manufacturing, where precision and efficiency became attainable goals for a broader range of users.
What is a CNC Machine Used for?
CNC machines are employed across various industries for a multitude of applications due to their precision and adaptability. They are primarily used for machining operations such as milling, turning, and drilling, which enable the creation of intricate parts and components with tight tolerances. In the automotive industry, CNC machines are crucial for manufacturing engine components, frames, and body parts. The aerospace sector relies on CNC technology for crafting lightweight, high-strength components like wing structures and fuselage elements.
Additionally, CNC machines are instrumental in the production of custom furniture, prototypes, and artistic pieces in the woodworking and manufacturing sectors. They also play a vital role in electronics, helping to create circuit boards and enclosures with precise specifications. The versatility of CNC machines makes them indispensable tools in modern manufacturing, allowing businesses to produce high-quality products efficiently while reducing waste and production time.
Who Are Machinists?
Machinists are skilled tradespeople who operate and maintain CNC machines, playing a vital role in manufacturing. They set up machines according to specifications, which includes installing tools, adjusting settings, and loading materials. Working closely with CNC programmers and engineers, machinists ensure that produced parts meet precise tolerances and quality standards.
In addition to running CNC equipment, machinists monitor operations during production, making adjustments to maintain accuracy and efficiency. They have a strong grasp of machining processes and can read technical drawings and blueprints. Problem-solving skills are crucial, as machinists troubleshoot issues, using their knowledge of machines and materials to deliver high-quality components. Their expertise ensures smooth workflows and optimal production outcomes, making them invaluable in the CNC machine industry.
What Controls a CNC Machine?
Introduction to CNC Machine Controls
CNC machines are controlled by a combination of hardware and software systems that work together to ensure precise and accurate operation.
The Role of the CNC Controller
At the heart of this control system is the CNC controller, which interprets the G-code—a programming language used to communicate instructions to the machine. This G-code dictates the movement of the machine’s axes, the speed of cutting tools, and various operational parameters.
Hardware Components
The hardware component typically includes stepper motors or servo motors that drive the movement of the axes, allowing for three-dimensional movement in X, Y, and Z directions. Additionally, feedback systems such as encoders provide real-time data to the controller regarding the position and speed of the machine components, automatically adjusting operations for any discrepancies.
User-Friendly CNC Software Interfaces
User-friendly software interfaces enable operators to create, modify, and export G-code or M-Code easily, incorporating CAM (Computer-Aided Manufacturing) software that can facilitate complex designs and optimizations.
Different Types of CNC Machines
CNC Machine Processes
CNC machines can be categorised into several cnc processing types, each designed for specific operations, thus expanding their versatility in manufacturing processes. Below are some of the common types:
Milling Machines
Milling machines employ a rotating spindle to remove material from a stationary workpiece. This process allows for the creation of complex shapes and intricate details through various milling tools that can cut, drill, and shape materials with precision.
Turning Machines
In turning machine tool operations, the workpiece is cylindrical and rotates while the spindle remains fixed. This method effectively removes material from the outer diameter of the workpiece, allowing for the production of uniform shapes such as shafts or fittings.
Plasma and Laser
Plasma and laser cutting machines offer advanced capabilities for cutting various materials with high precision and speed. Plasma cutters utilize a high-velocity jet of ionized gas to melt and blow away material, making them ideal for thick metal components. On the other hand, laser cutting employs a focused beam of light to achieve fine cuts with minimal distortion, making it suitable for both metal and non-metal materials. Both methods are widely used in industries requiring intricate cuts and detailed designs, such as aerospace, automotive, and fabrication.
Drilling Machines
Drilling machines work by cutting holes into the workpiece using a rotating drill bit. This essential operation is crucial for creating precise holes for assembly or fasteners in a wide range of components. View CNC Drilling >
Grinding Machines
Grinding machines utilise a rolling, abrasive wheel to remove small amounts of material from a workpiece. This process is key for achieving high-precision finishes, ensuring a smooth surface and meeting tight tolerances in manufactured parts. View CNC Grinding >
Sawing Machines
Sawing machines cut materials into parts using a blade, making them ideal for reducing large blocks of material into manageable sizes or preparing raw materials for further processing.
Finishing Operations
Finishing operations play a critical role in enhancing the surface quality of manufactured parts. This includes:
- Filing: A method that combines grinding and sawing, where light amounts of material are removed primarily for deburring edges.
- Polishing and Brushing: These processes involve the use of abrasives to create a smooth or shiny surface, enhancing the aesthetic and functional attributes of the final product.
Together, these CNC machinery types showcase the breadth of capabilities available in modern manufacturing, allowing for enhanced precision, efficiency, and quality across a multitude of applications.
What is a CNC Lathe?
A CNC lathe is a type of CNC machine specifically designed for turning operations, where a rotating workpiece is shaped by a stationary cutting tool. Unlike traditional lathes that require manual intervention, CNC lathes are computer-controlled, allowing for precise automation of the machining process. This technology allows manufacturers to create cylindrical parts with high accuracy, including shafts, bolts, and intricate designs.
Lathe machines can perform multiple functions, such as turning, facing, drilling, and threading, all within a single setup, significantly increasing efficiency and productivity. The advanced programming capabilities of CNC lathes also enable the production of complex geometries that would otherwise be challenging to achieve manually, making them an essential tool in modern manufacturing and industries ranging from automotive to aerospace.
What is a CNC Mill?
A CNC mill ( Also known as a CNC Milling machine ) is a highly versatile type of CNC machine that utilises rotary cutters to remove material from a stationary workpiece, creating precise shapes and intricate features. Unlike in conventional milling, where manual adjustments and operations are necessary, CNC mills are fully automated and controlled via computer programming. This automation provides superior accuracy and repeatability, allowing for the production of complex parts with tight tolerances.
CNC milling machines use a variety of operations, including drilling, tapping, and contouring, making them suitable for a broad range of materials such as metals, plastics, and wood. With the ability to execute multiple passes and adjustments without human intervention, CNC mills enhance productivity and efficiency, thereby revolutionising manufacturing processes across multiple industries.
CNC Mill vs. CNC Lathe
CNC mills and CNC lathes serve distinct functions in the manufacturing realm, with each machine offering unique advantages based on the type of workpiece and desired outcome. The primary difference lies in their operational mechanics: CNC mills utilize rotary cutters to remove material from a stationary workpiece, making them ideal for creating complex shapes and intricate detailing. In contrast, CNC lathes shape cylindrical workpieces by rotating them against a fixed cutting tool, which is best suited for producing uniform components like shafts, bolts, and various fittings.
When it comes to versatility, CNC mills excel in handling a variety of operations—such as drilling, tapping, and contouring—across various materials. This versatility allows manufacturers to take on multiple tasks in a single setup, enhancing efficiency. On the other hand, CNC lathes are specifically tailored for turning operations and can perform multiple functions like facing, drilling, and threading, thereby making them particularly effective for cylindrical parts. Ultimately, the choice between CNC mills and lathes depends on the specific manufacturing requirements, tooling capabilities, and the complexity of the parts being produced.
What is a 5 Axis CNC Machine?
A 5 axis CNC machine ( Multi Axis CNC Machine ) is an advanced type of CNC machining tool that allows for the movement of the cutting tool across five different axes simultaneously. This capability enables the machine to cut and shape parts with intricate geometries and complex angles that would be challenging, if not impossible, to achieve with traditional 3 or 4 axis machines. In a 5 axis setup, the workpiece can be rotated and tilted, while the cutting tool moves in multiple directions, enhancing precision and significantly reducing the number of setups required.
5 axis CNC machines are particularly beneficial in industries such as aerospace, automotive, and medical, where components often require intricate details and high tolerances. They are capable of producing highly detailed parts, including molds, dies, and complex structures, all while maintaining superior surface finishes. Additionally, the enhanced flexibility and efficiency of 5 axis machining can lead to shorter production times and reduced cycle times, making it a valuable investment for manufacturers aiming to improve their production capabilities.
By Rhododendrites - Own work, CC BY-SA 4.0, Link
What is a CNC Router?
A CNC router is a computer-controlled cutting machine that is commonly used for a wide variety of materials, including wood, plastics, composites, and even metal. Unlike lathes and mills that primarily focus on turning and milling operations, CNC routers are designed for cutting, shaping, and engraving flat materials, making them ideal for applications such as cabinet making, signage production, and artistic design. The machine operates by moving a router—an electric tool used for hollowing out an area in a hard material—through the three-dimensional space of the workpiece, following precise coordinates programmed into its computer control system.
CNC routers offer distinct advantages, including high speed, efficiency, and repeatability, allowing for the rapid production of intricate designs and detailed patterns. They typically feature large cutting tables that can accommodate sizable sheets of material, and they are equipped with multiple tool heads to facilitate various cutting techniques. The flexibility of CNC routers makes them essential in industries ranging from woodworking and cabinetry to aerospace and prototyping, where the ability to produce detailed components with precision and ease is paramount.
What are Universal CNC Machines?
Universal CNC machines are versatile and multifunctional machining tools capable of performing a wide range of operations, often combining the capabilities of various traditional machines into a single unit. These machines are designed to handle diverse tasks, such as milling, turning, drilling, and engraving, making them ideal for a variety of applications across different industries. The adaptability of universal CNC machines is facilitated by their advanced software, which allows for complex programming and automation, enabling operators to switch between different processes with relative ease.
This flexibility significantly enhances productivity and efficiency by reducing the need for multiple machines, streamlining workflow, and minimizing setup times. Universal CNC machines are particularly beneficial in small to medium-sized manufacturing environments where space and budget constraints may limit the use of specialized equipment. Their ability to work with various materials, including metals, plastics, and composites, allows manufacturers to tackle diverse projects, making universal CNC machines an essential asset for modern production facilities.
What is a CNC Plasma Cutter?
A plasma cutter is a sophisticated tool used to cut through electrically conductive materials by employing a high-velocity jet of ionized gas, known as plasma. This technology harnesses an electric arc to create extreme heat, melting the metal, while the pressurised gas blows the molten material away from the workpiece. Plasma cutters are renowned for their speed and precision, making them ideal for cutting thick metals such as steel, stainless steel, and aluminium with minimal distortion or heat-affected zones. The ability to adjust settings allows operators to cut at varying thicknesses and intricate designs, making plasma cutters invaluable in industries such as metal fabrication, automotive repair, and construction. Furthermore, the portability of many plasma cutting systems enhances their practicality for both workshop and field applications, ensuring versatility in various operational environments.
What is a CNC Laser Cutter?
A laser cutter is a cutting-edge machine that uses focused laser beams to cut or engrave materials with exceptional precision. By directing high-intensity light energy onto the workpiece, laser cutters heat the material until it melts or vaporises, allowing for intricate designs and detailed shapes to be achieved with minimal kerf. This technology is highly versatile, capable of cutting through various materials including metals, plastics, wood, and fabric, making it suitable for applications ranging from industrial manufacturing to fine arts and crafts.
One of the primary advantages of laser cutting is its ability to produce clean, precise edges without the need for secondary processing, reducing waste and improving overall efficiency. Additionally, laser cutters can be programmed to handle complex geometries and patterns quickly and accurately, which significantly speeds up production times while ensuring consistency in quality. As a result, laser cutting has become an essential tool in many sectors, including aerospace, automotive, signage, and architectural design, due to its remarkable versatility and accuracy.
Laser vs. Plasma Cutter
When comparing laser cutters and plasma cutters, both technologies have distinct advantages that cater to different manufacturing needs. Laser cutters are renowned for their exceptional precision and ability to create intricate designs with minimal kerf. They excel in cutting thinner materials effectively and producing clean, smooth edges, which often eliminates the need for secondary processing. This makes them ideal for applications like fine arts, detailed signage, and intricate metalwork and makes it easier on the CNC operator.
On the other hand, plasma cutters shine when dealing with thicker materials, such as heavy steel or stainless steel, where their high-speed cutting and ability to navigate large pieces of metal become advantageous. Plasma cutting is generally faster than laser cutting, especially for thicker workpieces, making it a preferred choice in high-volume metal fabrication and construction industries. However, the edges produced by plasma cutters may require additional finishing processes to achieve the same cleanliness as laser-cut edges. Ultimately, the choice between laser and plasma cutting depends on the specific requirements of the project, including material type, thickness, desired precision, and production speed.
What is an EDM Machine?
An EDM (Electrical Discharge Machining) machine is a precision tool used to remove material from a workpiece through the use of electrical discharges or sparks. This process occurs in a controlled environment, where a series of rapid electrical discharges are generated between an electrode and the workpiece, resulting in the melting and evaporating of the material. EDM is particularly effective for machining hard materials that are difficult to work with by traditional methods, such as high-strength alloys and hardened steel.
There are two primary types of EDM machines: sinker EDM, which uses a shaped electrode that matches the desired geometry of the final part, and wire EDM, which employs a thin, electrically charged wire to cut through the material. Both methods offer high precision, intricate shapes, and smooth surface finishes, making them invaluable in industries such as aerospace, automotive, and tool-making, where accuracy and detail are paramount.
By NezzerX at English Wikipedia - Own work, Public Domain, Link
How Do You Program a CNC Machine?
Programming a CNC machine involves several key steps that enable the machine to perform precise operations on the workpiece. The first step is to create a Computer-Aided Design (CAD) model of the part that needs to be manufactured. Once the design is finalised, it is imported into Computer-Aided Manufacturing (CAM) software, which translates the CAD model into a set of instructions for the CNC machine, known as G-code.
What is G-Code?
G-Code, also referred to as Gerber Code or simply “G,” is the standard programming language used to control CNC (Computer Numerical Control) machines. It consists of a series of commands that dictate the movement and operation of the machining tool, allowing for precise control over the machining process. Each G-Code command starts with the letter “G” followed by a number, indicating a specific function, such as moving the machine in a straight line (G00 for rapid positioning) or cutting along a specified path (G01 for linear interpolation).
G-Code instructions are typically generated through CAM software, translating intricate CAD designs into the machine’s language. This enables the CNC machine to interpret the movement, speed, and other operational parameters necessary to accurately produce the desired part. Additionally, G-Code can be customised to suit different machines and tooling configurations, offering versatility across various manufacturing applications. Understanding G-Code is essential for machinists and operators, as it allows for optimisation of machining processes, troubleshooting, and enhancement of production efficiency.
What is M-Code?
M-Code, or Miscellaneous Code, is a crucial component of CNC programming that complements G-Code by providing commands that control various machine functions not related to the movement of the cutting tool. These commands typically manage aspects such as coolant control, spindle speed, tool changes, and program stops. For example, M03 is used to activate the spindle in a clockwise direction, while M05 is employed to stop the spindle entirely.
M-Codes are often machine-specific, meaning that while some commands may be standard across different CNC machining operations, others can vary based on the manufacturer or the machine type. This specificity requires operators to be familiar with the M-Code conventions for their particular machine. Effective use of M-Code is essential for optimising machining processes, ensuring that all auxiliary functions are executed correctly and efficiently, ultimately contributing to improved production quality and efficiency.
G-Code vs. M-Code
Understanding the differences between G-Code and M-Code is essential for anyone involved in CNC programming and operation. G-Code primarily focuses on the movement and positioning of the cutting tool, detailing how the machine should execute the machining process. It determines the path, speed, and feed rate of the tool as it interacts with the workpiece, enabling precise control over the manufacturing output.
In contrast, M-Code is responsible for managing the auxiliary functions of the CNC machine that support the operational process but do not directly control the tool’s movement. This includes commands for activating cooling systems, adjusting spindle speeds, and executing tool changes. While G-Code commands are typically universal across CNC machines, M-Codes may vary significantly between different manufacturers, making it crucial for operators to be well-versed in the specific M-Code functions relevant to their equipment. Together, G-Code and M-Code form a comprehensive programming system that allows for efficient and precise CNC machining.
Who are CNC Programmers?
CNC programmers are skilled professionals responsible for creating and managing the code that controls CNC machines. They play a vital role in the manufacturing process by translating complex product designs into precise instructions that guide the machines in executing tasks such as cutting, milling, and engraving. CNC programmers often possess a strong background in engineering, mathematics, and computer-aided design, enabling them to interpret technical drawings and specifications effectively.
Typically, CNC programmers work closely with engineers and machinists to ensure that the products meet quality standards and production timelines.
Industries that Use CNC Machine Tools
CNC machines are employed along side CNC machinist or also known as machine operators across a wide array of industries due to their precision and efficiency in manufacturing processes. One of the primary sectors is the aerospace industry, where exact specifications are crucial for components such as aircraft frames and parts, necessitating high-quality machining to ensure safety and performance. The automotive industry also heavily relies on CNC technology for producing everything from engine parts to intricate interior components, allowing for high-volume production with consistent quality.
CNC Machines Streamlines Operations
Moreover, the manufacturing sector benefits significantly from CNC machines, as they streamline operations for producing machinery, tools, and industrial parts. In the medical field, CNC machining is used to create surgical instruments and implantable devices, where precision is vital for both functionality and patient safety. Lastly, the woodworking and furniture industry utilizes CNC machines to create custom designs and intricate carvings, enhancing both production capabilities and aesthetic appeal. This diverse application across industries highlights the indispensable role of CNC machines in modern manufacturing.
Industry | Type of CNC Machine | Typical Products/Services |
---|---|---|
Aerospace | CNC Milling Machines | Aircraft components, engine parts, landing gear |
Automotive | CNC Lathes, CNC Milling Machines | Engine blocks, transmission components, custom car parts |
Medical | CNC Swiss Machines, CNC Milling Machines | Surgical instruments, prosthetics, implants |
Electronics | CNC Routers, CNC Drilling Machines | Circuit boards, enclosures, connectors |
Furniture | CNC Routers, CNC Milling Machines | Custom furniture, cabinetry, decorative wood pieces |
Metalworking | CNC Plasma Cutters, CNC Laser Cutters | Metal fabrication, custom metal parts, tool and die making |
Jewelry | CNC Engraving Machines | Custom jewelry, engravings, intricate designs |
Marine | CNC Lathes, CNC Milling Machines | Boat hulls, propellers, marine engine components |
Construction | CNC Routers, CNC Milling Machines | Architectural components, custom building materials |
Plastic and Rubber | CNC Milling Machines, CNC Routers | Plastic parts, molds, rubber components |
Signage | CNC Routers, CNC Laser Cutters | Custom signs, billboards, engraved signs |
Tool and Die Making | CNC Milling Machines, CNC Grinding Machines | Molds, dies, precision tools |
Renewable Energy | CNC Milling Machines, CNC Lathes | Wind turbine components, solar panel frames |
Agriculture | CNC Plasma Cutters, CNC Lathes | Tractor parts, agricultural machinery components |
Artwork | CNC Routers, CNC Engraving Machines | Sculptures, custom art pieces, intricate designs |
Major CNC Machine Brands
The CNC industry features several prominent brands known for their innovation, quality, and reliability. Among them, Haas Automation stands out as a leader in the production of CNC vertical and horizontal machining centres, offering a strong combination of performance and affordability. Mazak is another significant player, renowned for its advanced technology and diverse range of CNC systems tailored for various manufacturing needs, including turning and milling applications.
Below you will find a list of major brands by the type of CNC machine they sell and country of origin
Brand | Types of CNC Machines | Country of Origin | Popular Models | Website |
---|---|---|---|---|
Mazak | CNC Lathes, CNC Milling Machines, CNC Multi-Tasking Machines | Japan | INTEGREX Series, VARIAXIS Series, QTU Series | https://www.mazak.com |
Haas Automation | CNC Lathes, CNC Milling Machines, CNC Routers | USA | VF Series, ST Series, GR Series | https://www.haascnc.com |
DMG Mori | CNC Lathes, CNC Milling Machines, CNC Grinding Machines | Germany/Japan | DMU Series, NLX Series, DMC Series | https://www.dmgmori.com |
Okuma | CNC Lathes, CNC Milling Machines, CNC Grinding Machines | Japan | GENOS Series, LB Series, MU-V Series | https://www.okuma.com |
FANUC | CNC Controllers, CNC Robotics, CNC Lathes | Japan | ROBODRILL, ROBOSHOT, ROBONANO | https://www.fanucamerica.com |
Siemens | CNC Controllers, CNC Systems | Germany | SINUMERIK 840D, SINUMERIK 828D | https://new.siemens.com/global/en.html |
Hurco | CNC Lathes, CNC Milling Machines | USA | VMX Series, TMX Series, VCX Series | https://www.hurco.com |
EMCO | CNC Lathes, CNC Milling Machines | Austria | Concept Turn, MaxxMill, Emcoturn | https://www.emco-world.com |
Makino | CNC Milling Machines, CNC EDM Machines | Japan | PS Series, V Series, U Series | https://www.makino.com |
Brother | CNC Milling Machines, CNC Tapping Centers | Japan | Speedio Series, TC Series | https://www.brother-usa.com |
Doosan | CNC Lathes, CNC Milling Machines | South Korea | PUMA Series, DNM Series, Lynx Series | https://www.doosanmachinetools.com |
Kitamura | CNC Milling Machines, CNC Lathes | Japan | Mycenter Series, MedCenter5AX | https://www.kitamura-machinery.com |
Mori Seiki | CNC Lathes, CNC Milling Machines | Japan | NL Series, NH Series, NT Series | https://www.dmgmori.com |
Materials Used on CNC Machines
CNC machines are capable of processing a wide variety of materials, making them versatile tools in the manufacturing landscape.
Metals
Commonly used materials include metals such as aluminum, steel, brass, and titanium, each requiring specific machining techniques to achieve desired results. Aluminum, valued for its lightweight and corrosion-resistant properties, is frequently used in aerospace and automotive applications. Steel, known for its strength and durability, is often employed in heavy machinery and structural components.
Plastics
In addition to metals, CNC machines can work with various plastics, such as acrylic, nylon, and polypropylene. These materials are popular in industries ranging from consumer goods to medical devices, due to their lightweight and easy machinability.
Composite Materials
Furthermore, CNC technology is adept at handling composite materials, which combine different substances to enhance strength and reduce weight, especially in aerospace applications.
Wood
Wood is another significant material processed by CNC machines, particularly in the furniture and cabinetry industries. The precision offered by CNC allows for intricate designs and high-quality finishes.
Overall, the adaptability of CNC machining to different materials is a key factor in its widespread adoption across diverse sectors, enabling manufacturers to meet specific requirements and maintain high standards of production quality.
Type of CNC Machine | Materials | Examples of Products |
---|---|---|
CNC Milling Machines |
|
|
CNC Lathes |
|
|
CNC Routers |
|
|
CNC Laser Cutters |
|
|
CNC Plasma Cutters |
|
|
CNC Grinding Machines |
|
|
CNC Swiss Machines |
|
|
Average Price of a CNC Machine
The price of CNC machines can vary widely based on factors such as size, complexity, capabilities, and the specific brand manufactured. Entry-level CNC machines, often used by smaller machine shops. hobbyists or small businesses, typically range from $2,000 to $20,000. These common CNC machines are suitable for lighter tasks and smaller-scale production. Mid-range CNC machines, offering more advanced features and additional precision, generally fall within the $20,000 to $100,000 range, making them ideal for larger workshops and manufacturing operations.
Advanced CNC Machine Pricing
High-end CNC machines, designed for intricate projects in industries like aerospace and automotive, can cost from $100,000 to over $500,000. These machines often come equipped with advanced technology, automation capabilities, and extensive support for complex machining tasks. Ultimately, the choice of CNC machine should align with the specific production needs and budget constraints of the buyer, ensuring that investment translates into efficient and effective manufacturing processes.
Type of CNC Machine | New Price (2023/2024) | Used Price (2023/2024) | Typical CNC Brands | Price Trend (Last 5 Years) |
---|---|---|---|---|
CNC Milling Machines | $50,000 - $200,000 | $20,000 - $100,000 | Haas, DMG Mori, Mazak, Makino | +15% |
CNC Lathes | $40,000 - $150,000 | $15,000 - $80,000 | Okuma, Haas, Doosan, Mazak | +10% |
CNC Routers | $5,000 - $150,000 | $3,000 - $80,000 | ShopBot, Biesse, AXYZ, Thermwood | +8% |
CNC Laser Cutters | $15,000 - $300,000 | $10,000 - $150,000 | Trumpf, Bystronic, Mazak, Amada | +12% |
CNC Plasma Cutters | $10,000 - $200,000 | $5,000 - $100,000 | Hypertherm, Lincoln Electric, Esab, MultiCam | +7% |
CNC Grinding Machines | $50,000 - $500,000 | $25,000 - $250,000 | Studer, ANCA, Makino, Okuma | +15% |
CNC Swiss Machines | $100,000 - $500,000 | $50,000 - $250,000 | Tornos, Citizen, Star, Tsugami | +18% |
Used CNC Machines VS New CNC Machines
When evaluating CNC machines, one must consider the advantages and disadvantages of purchasing used versus new equipment. Used CNC machines can offer substantial cost savings, often being available at significantly lower prices than their new counterparts. This affordability makes them an attractive option for small businesses or startups looking to enter the manufacturing landscape without hefty investments. Additionally, many used machines have been well-maintained and come equipped with valuable accessories that enhance functionality.
However, buying used machines may present challenges, such as limited warranties, uncertain maintenance histories, and potential outdated technology that might not support the latest software or machining processes. Conversely, new CNC machines provide the benefits of the latest technology, improved precision, and extended warranties, ensuring reliability and performance. They often incorporate advanced features such as automation and enhanced user interfaces, which can boost productivity and ease of operation.
Ultimately, the decision between used and new CNC machines should be influenced by budget, production requirements, and long-term business goals, ensuring the chosen solution aligns with the specific needs of the manufacturing environment.
Used CNC Machines | New CNC Machines | |
---|---|---|
Pros |
|
|
Cons |
|
|
Ideal For |
|
|
Automate a CNC Machine
CNC machines can be automated to enhance production efficiency and reduce manual intervention. Automation in CNC machining typically involves integrating advanced technologies such as robotics, conveyors, and software systems that enable the automatic loading and unloading of materials, as well as real-time monitoring of machine performance. This not only streamlines workflows but also minimizes the risk of human error, ensuring consistent quality in the manufacturing process.
Moreover, automated CNC machines can operate continuously, allowing for unattended machining hours, which significantly increases output and optimises production schedules. With the advancement of Industry 4.0, many manufacturers are leveraging smart automation solutions, including IoT connectivity and data analytics, to further enhance the capabilities of CNC machines. These innovations enable manufacturers to gather insights on machine performance, predictive maintenance, and process optimisation, ultimately leading to improved operational efficiencies and reduced production costs.
Lights Out Manufacturing with CNC Machines
Lights out manufacturing refers to a production strategy where operations are conducted with minimal human intervention, often running unattended during non-operating hours, such as nights or weekends. This approach leverages CNC machines’ capabilities to operate autonomously, enabling manufacturers to maximize productivity while minimizing labor costs. By utilising advanced automation and robotics, lights out manufacturing allows for the continuous operation of CNC machines, resulting in increased output and efficiency.
Implementing a lights out manufacturing strategy requires careful planning, including the use of high-quality machinery that can handle extended periods of operation without supervision. Additionally, the integration of automation systems, such as automated material handling and real-time monitoring software, becomes essential to monitor the CNC machines’ performance and ensure consistent product quality. Though the initial setup costs and the complexity of integrating such systems may pose challenges, the long-term benefits include reduced production costs, improved machine utilisation, and the ability to maintain a competitive edge in the market. As manufacturers embrace Industry 4.0 technologies, lights out manufacturing stands to revolutionize CNC machining’s role in achieving seamless and efficient production workflows.
CNC Machine Technology Today
Evolution of CNC Machine Technology
The landscape of CNC machine technology has evolved significantly with the integration of networking and information technology, enabling smarter and more efficient manufacturing processes. Modern CNC machines now often come equipped with Wi-Fi and web connectivity features, allowing them to communicate with other devices and systems seamlessly. This connectivity facilitates remote monitoring and control, enabling operators to make adjustments, receive alerts, and perform diagnostics from anywhere, enhancing overall productivity and reducing downtime.
Integration of Robotics
In addition to improved connectivity, the incorporation of robotics into CNC machining has transformed production capabilities. Collaborative robots, or cobots, work alongside human operators, handling repetitive or dangerous tasks, which not only boosts efficiency but also enhances workplace safety. These robots can be programmed easily to adapt to different tasks, offering flexibility in manufacturing processes.
Advancements in AI and Machine Learning
Furthermore, advancements in artificial intelligence and machine learning allow CNC machines to learn from their environments, optimizing their operations for more precise results and reduced waste.
The Role of Software Solutions
Alongside these developments, the continuous evolution of software solutions, particularly those that leverage data analytics and cloud computing, plays a vital role in optimizing CNC operations. Manufacturers can now analyze vast amounts of data related to machine performance, production rates, and maintenance needs, leading to predictive maintenance strategies that mitigate equipment failures.
Future of Smart Manufacturing
As smart manufacturing continues to grow, the integration of advanced technologies within CNC machining ensures that manufacturers remain competitive, agile, and responsive to market demands.
Industry 4.0
Industry 4.0, known as the Fourth Industrial Revolution, is a transformative movement that integrates digital technologies, automation, and data exchange to create smart factories. Key components include the Internet of Things (IoT), artificial intelligence (AI), robotics, and advanced data analytics, which enhance manufacturing processes by enabling real-time decision-making and seamless communication among machines, products, and humans. This interconnectedness boosts flexibility, efficiency, and productivity while allowing for personalized products and improved supply chain management.
The impact of Industry 4.0 on CNC machines is profound, as they now integrate with IoT devices for real-time data exchange, enhancing monitoring and predictive maintenance. The use of AI and machine learning in CNC machining optimizes cutting processes, increases precision, and reduces waste, leading to cost-effective operations. As manufacturers embrace these technologies, CNC machining evolves, paving the way for agile, efficient, and sustainable smart factories.
Conclusion
In conclusion, CNC machine technology has transformed the manufacturing landscape, offering manufacturers essential tools to boost productivity and reduce costs. The choice between new and used machines, along with the integration of automation, robotics, and smart manufacturing solutions, empowers businesses to streamline operations effectively. By embracing IoT connectivity, predictive maintenance, and lights-out manufacturing, companies can respond swiftly to market demands. As we move into the era of Industry 4.0, manufacturers leveraging these advancements will not only maintain a competitive edge but also create a more efficient, reliable, and sustainable production environment. The future of CNC machining is promising, fueled by a dedication to continuous improvement and operational excellence.